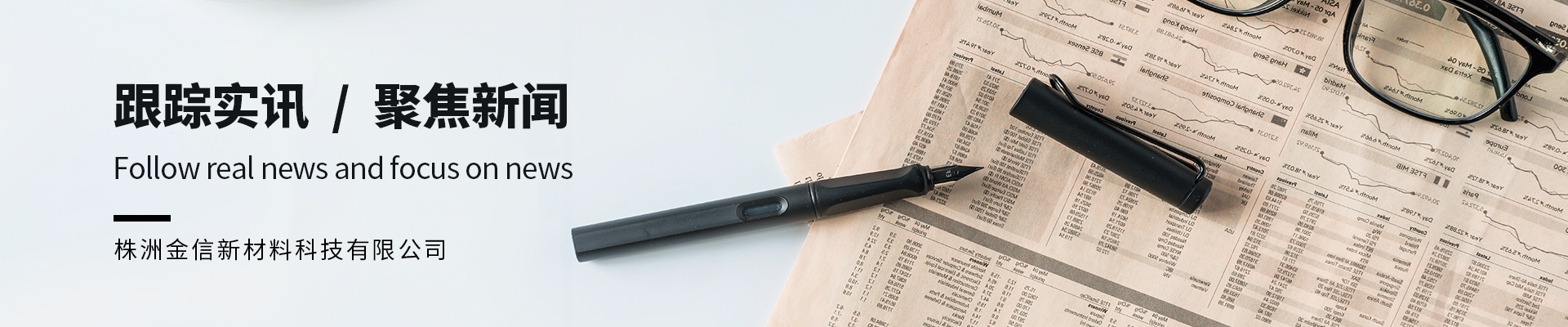
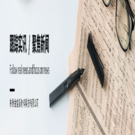
在現代工業生產中,軋輥作為金屬加工的核心部件,其性能直接影響產品質量和生產效率。硬質合金軋輥憑借卓越的耐磨性、耐高溫性和抗腐蝕性,成為鋼鐵、有色金屬、造紙、塑料等行業的首選材料。我們將深入解析硬質合金軋輥的技術優勢、應用場景及行業趨勢,助力企業了解這一關鍵技術的價值。
硬質合金軋輥主要由碳化鎢(WC)和金屬鈷(Co)組成,通過粉末冶金工藝制成。碳化鎢作為硬質相,賦予軋輥極高的硬度(可達 86-93HRA)和耐磨性,而鈷作為粘結相,提供韌性和抗沖擊性。這種 “剛柔并濟” 的材料結構,使其在高溫、高壓環境下仍能保持穩定性能。
制造工藝方面,冷等靜壓成型技術通過高壓油體均衡傳壓,確保坯體密度均勻;燒結熱等靜壓技術則在真空環境下消除孔隙,提升材料致密度,使軋輥壽命較傳統工藝提升 5-10 倍。例如,CIC(澆鑄式硬質合金)技術將碳化鎢與球鐵熔合,結合鍛鋼軸的強韌性,實現了成本與性能的優化平衡。
1. 耐磨性與壽命提升
硬質合金軋輥的硬度是傳統合金鑄鐵軋輥的 3-5 倍,耐磨性提高 5-10 倍。以鋼鐵行業為例,硬質合金軋輥在棒材、線材軋制中,單次修磨可軋制 3000 噸以上鋼材,較普通工具鋼提升 20-50 倍。這不僅減少了停機換輥頻率,還降低了維護成本,提高設備綜合效率(OEE)。
2.高精度與穩定性
在冷軋帶肋鋼筋生產中,硬質合金軋輥可實現肋痕清晰、尺寸精度誤差小于 0.1mm 的軋制效果,顯著提升產品表面質量和成材率。航空航天領域對零部件精度要求極高,硬質合金軋輥憑借納米級加工能力,確保鈦合金、高溫合金等材料的精密成型。
3. 耐高溫與抗熱疲勞
硬質合金軋輥在 800℃高溫下仍能保持穩定性能,抗熱裂紋能力優于傳統材料。例如,YGR 系列軋輥通過優化鈷含量和晶粒結構,可承受中低速高扭矩工況,避免斷裂風險。
典型應用場景:
熱銷產品